Decarbonising Distilleries - Meeting the Net Zero Challenge
Our Principal Engineer, Andrew McGhee applies his 25 years of energy sector and distillery engineering experience to look at some of the answers.
We all know that emissions of CO2 have to be greatly reduced over the next very few years, and that distillers everywhere are working hard on how to achieve this. The last Environmental Strategy Report from the Scotch Whisky Association shows the distilling industry leading the charge, reporting that the 2020 target for reducing fossil fuel use has been smashed, with 39% of primary energy now coming from non-fossil fuels.
But there’s no getting away from the fact that distilling is an energy intensive process, so what is the beleaguered energy or environment manager to do? The good news is that there are lots of options out there. That’s also the bad news – because no single one of these options is “the best” in every situation. So, there’s a need for careful assessment (by that beleaguered energy manager) on a case-by-case basis.
We (Reheat) believe that there is a place for all of the options; that no individual option can do it all. If anyone tells you that that theirs is the best solution in every case, then heed caution and consult an engineer or sustainable energy professional.
Maximising energy efficiency across every stage of a process should be a given. Your insulation should be good, your steam leaks should be eliminated, and waste heat should be recovered and beneficially reused wherever practicable. Apart from that, there are dozens of ways of reducing energy use, from the cheap and simple, to the hugely complex and expensive.
Which ones are justified (or justifiable) on any particular site depends on the size of the site and the price of your energy, amongst other things. But one universal truth is that however much you work on energy efficiency improvement, you’re still going to need a source of energy which is as close to zero carbon as possible.
So, what are the main options to consider to achieve carbon neutral heat in a distillery?
Electrification
It’s perfectly possible to generate heat from electricity, either directly or by using a heat pump. Electrical heat is clean and easy – we use it every time we make a cup of tea or coffee. Some will tell you it’s 100% efficient, but of course that is misleading. The main problems with electrical heat are that it’s expensive, and the UK’s power grid simply can’t support generation and distribution on the scale required to fully decarbonise our heat, not to mention our transport.
The price problem can be reduced with high temperature (steam raising) heat pumps, however, they’re not widely used or proven yet in industrial applications. Also, to qualify for RHI support, heat pumps can only use air or ground source – not waste process heat, and air/ground source high temperature heat pumps have low coefficients of performance due to the high temperature uplift required.
The other broader problem with the electrification of heat is a looming power generation squeeze in the UK. Six of the UK’s 7 existing nuclear power stations and all of the coal fired stations are expected to shut down within the next 10 years, although there should be a new nuclear plant coming online soon – Hinkley C in Somerset, which is projected to begin providing power to the grid in around 2026, and will provide around 7% of the UK’s electricity needs. But with the UK’s current nuclear fleet providing around 20%, you can see the problem. Add to that an increasing demand from the electrification of transport, and the power squeeze is apparent.
Increased renewable generation – especially offshore wind – will fill some of the gap, but it’s doubtful whether the grid (generation or distribution) can support the widespread deployment of heat electrification without huge infrastructure investment. Electrification of heat could be viable if you can generate power locally – tidal power on Islay or Scapa Flow for example, but these sorts of options are limited in scope and scale. So, there is a place for some electrification of heat, but it is by no means the panacea for the 2020s that some claim.
Hydrogen
Great fuel, zero emissions – what’s not to like? Well, there is currently nowhere near enough of it to go round! You can make it from water and electricity, but the poor energy conversion efficiency means you would be better off just using the electricity directly. Really, hydrogen is an energy storage medium – not an energy source. It’s also very expensive at the moment.
As the hydrogen market develops over the next few years, supply will increase and prices will drop, but it’s probably a decade or more away from helping that poor energy manager, and the UK government has big ambitions for using hydrogen in the existing fossil gas grid. The hydrogen industry needs support because it’s certainly a part of the future energy mix, but it’s not ready to help many people with 2030 emissions targets to meet, particularly if they’re off the gas grid.
Biomass
People have been burning wood for thousands of years to raise heat, and in 2023 it still constitutes the world’s largest non-fossil source of energy. It’s renewable, the technology is proven, there’s an established supply chain, and you can have a system up and running in a year.
As this opinion is coming from a biomass company, you’d expect us to claim that it’s the answer to everything, right? Well, no, we don’t think it’s for everyone. Again, there’s not enough wood available at present to cater for the entire distilling sector, and you really want to be in an area with an established forestry and wood products industry, because wood fuel is bulky. We wouldn’t recommend it in Shetland for example, but there’s no escaping the fact that wood is without doubt one of the most cost-effective emission reduction strategies which can be implemented at scale now.
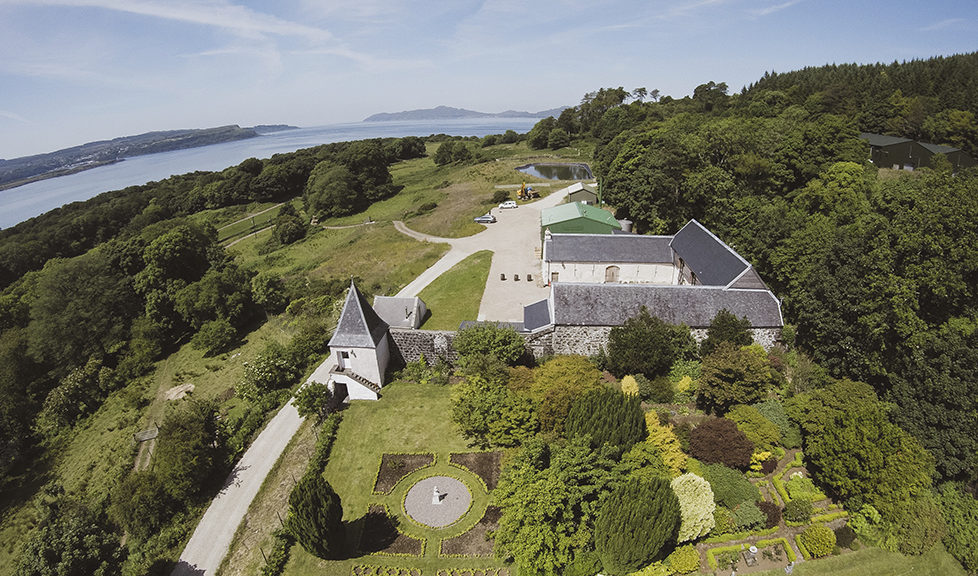
Biogas/bio-propane
Both natural gas and LPG (propane) can be manufactured from biogenic origins, so that the CO2 released on combustion has previously been drawn from the atmosphere by plants. Both are chemically identical to their fossil equivalents, but again (are you getting the pattern yet?) there is not enough of either material available to satisfy the needs of the whole distilling industry.
Vegetable oils can also displace fuel oil in boilers for steam generation. Some oils are cost competitive with fossil oil and proven in industrial application. They do have one or two operational problems, but nothing that can’t be overcome. However, the supply of vegetable fuels oil is very limited, and heat users will have to compete with the transport sector for the available resource.
Geothermal energy
The deeper you drill, the hotter it gets. Unfortunately, to get steam you have to go really deep, and the upfront capital cost gets quite daunting. If you have a distillery in Iceland or Turkey, you probably know about this already, but there are a few areas in the UK with real geothermal potential. Worth checking out, but entirely dependent on local geology.
Biogenic carbon capture
For every 100 tonnes of CO2 which goes up the chimney from the boiler, over 30 tonnes is vented cold and pure from the fermentation process. That cold pure CO2 is ideal for re-use or sequestration. You have to be careful where that CO2 goes, but with geological sequestration projects alive and kicking in the UK, there is potential there. Unfortunately, it’s probably too far out for your 2030 targets, but do I dare suggest that whisky production could viably have negative emissions in the future by making use of this mechanism?
Alternative raw materials
Pea gin anyone? A tip of the hat to Arbikie Distillery in Angus, but this is probably not able to be rolled out on a large scale – and definitely not in the making of Scotch Whisky!
The main point here is that there isn’t enough of any one of these resources to supply all of Scotland’s distilleries, but most or all of these solutions are required if the industry – and not just individual distilleries – is to achieve carbon neutrality. In 2021, the Scotch Whisky Association set out its sustainability strategy that demonstrates how the industry will achieve Net Zero emissions in its own operations by 2040. With a strong start, it will be interesting to see what decarbonisation methods are taken up over the coming years.
______________________
Banner image: Credit Nc'nean Organic Whisky Distillery